New page on NEW GROWTH WOOD - LUMBER & CEDAR SIDING AND ROOFING - LIMITED LIFE EXPECTANCY AND QUICKER DETERIORATION.
[ add comment ] ( 125 views ) | [ 0 trackbacks ] | permalink |





It is clear that a near 100% New Growth Wood usage is well under way in the new construction market. Quite certainly, the drive is present to produce new growth woods and to have them grow faster than ever before. This seems to have begun in earnest in post WWII time, as there was a surplus in war equipment, increase in demand for home building, and an increase in ecological concerns.
Not knowledgeable of the intricacies of the lumber and wood felling and growth industries, I can only comment on the results of the building industry and the apparent rotting potential of certain eras of the building industry. The rumors are that so called “New Growth” wood includes a faster growing product and the very limited information seems to support this and is assumed as fact among my contemporaries. I have read positive spin on the cutting of timber “to make room for New Growth” in the incidences of insect infiltration. I have run into previously insect damaged woods that have actually been installed onto home in sidings and trim. The issue I have that provides much angst for consumers is the predictable failure of many woods used within the industry.
Industry professional sales personnel from the few lumber conglomerates refuse to discuss the topic or they deny any knowledge of any such issues. This could be the result of the companies’ representatives being undereducated and employed in a low pay representative role, much like the manufacturer representatives described earlier. At several inquiries and diligent follow up, especially of the Cedar Industry, I was referred to higher-ups within the industry that had, what I considered cover stories for wood roof and siding failures. It seems that New Growth Woods, along with damaged lumber has been in supply for the last two decades as witnessed by a nearly 100% failure rate of exterior Cedar and some softwood trim materials.
From an end user’s field observation, I have always had a number in my mind. The number of years, counted backward as the age of a home sided or roofed in wood, primarily cedar, represented the stated timeframe in which my daily estimate excursions would show failure in these claddings and roofing. Many reasons again were assumed and manufactured, in my opinion to explain to the consumer the reason for such failures. Generally a number is in my mind, currently 20 years, where a home is on the cusp of that “New Growth” timeframe. It is very common, almost certain that if a homeowner has a home constructed in timeframe listed, currently 20 years back or less, sided or roofed in cedar, it will be shot, for lack of other words. The material appears to be dry and even a skeleton of itself, crushing upon any pressure applied. Those at the conglomerates associations have given excuses such as “Cell Collapsure,” for this phenomenon. This “Cell Collapsure,” or so it is called is supposedly a condition where wet cedar is shipped quickly into an arid region, such as Arizona and the resulting quick thaw/dry causes the loss of the natural acids and oils that protect the wood. I do not believe that this excuse or any other made-up excuse can cover the obvious, bad product. “New Growth,” is the term that applies as it is nearly 100% and we do recommend replacement.
Heartwood is the dense part of the cedar that is used in good quality roofing and siding. When installing roofing, it is common to discard the Sapwood Shakes, usually about 20% of the #1 grade wood roofing. When siding with full boards, the Sapwood is often used, as throwing it away would be a large waste and not cost effective. My estimation of the dilemna is “New Growth” wood is felled and made into product as a matter of practice. The associations are touting their treatment processes, but I have no faith in the materials produced in today’s modern exterior natural wood marketplace. I have seen nothing but failure and heard nothing but ridiculous excuses. New Growth wood has less Heartwood, as it is less mature. At least 100 years is required at minimum for good quality cedar.
If given the interest in reforestation only reaching back to the 1940’s, it seems clear that about the early 1980’s became a need that exceeded Old Growth supplies. Either for this reason or a combined effort from the environmentalists caused the felling of the New Growth from the 1940’s. Given the modern methods rumored to be hybrids, fertilizers and controlled growth, often called by slang terminology, “trees on steroids,” the cutting of the New Growth forests would seem practical and even patriotic. The result was not patriotic and certainly not practical. I see no evidence of any improvement within the industry.
Once a few years back, I came under the realization that this phenomenon is not limited to cedar. I was on an estimate in South Jersey in a community of about 22 years. At that time, my number (you will recall, the “timeframe” above) was about 17 years. The home was sided in wonderful cedar clapboard. At four inch exposure, it was beautiful, but the homeowner had trouble with keeping paint on the siding. I did not recommend a residing as the home did not require it. I did urge an interior vapor barrier be installed or a painting of the inside walls and ceilings with a vapor barrier paint (more on this later).
While I carefully inspected the home (as I am always learning something) I ventured around the back where I was speaking to the homeowner about the condition of even the trim, a softwood brick-molding. As I grabbed a piece of a window sill in the rear, it crumbled in my hand. I was surprised, as this was unlike all of the other sills I had inspected. I thought that, perhaps a storm window had been on the home, and caused interior moisture buildup, but this was not the case as none of the windows had storms. I moved up to the brick-molding. It was toast! No insect damage was evident and all brick-moldings on this section were gone. They were carefully painted and the paint seemed to be holding the wood together. The homeowner said, “Oh, that is the addition.” A small addition had been added onto the home so perfectly that a trained eye could not tell any difference. The siding even looked from the same stock and showed the exact condition as the original home. The owner stated that the addition was reportedly done several years after the main house. The number 17 came to mind, “Bingo”, I thought,”but what about the siding?” The siding must have been from the old stock, or it was just on the “cusp.” This was the beginning of the realization that the “New Growth” phenomenon was not limited to cedar. So my nagging question is “What about all the homes constructed in the last 20 years, the framing, etc.?” Wow, the implications may be huge, if I am correct. So, when I venture to the big box home stores, I look over the ends of the 2x4’s for density, wondering if the New Growth phenomena will cause havoc to the homes built in the latter days.
I do know that since the use of temporary sidings, of which I will describe later on in the book, any leak can cause major damage in the framing of a home built over the last 20 years, or so. Possibly, not only the fact that a leak has occurred, but the quality of the lumber has contributed to the significance of the damage.
We have resided old homes built as far back as 1703 (our oldest reside job to date), where no paint was evident on the wood trim, but no rot was found on the structure. Last year we sided a home built in 1703, among many other very old homes. The common phenomena observed was the lack of rot and the lack of insect damage. The woods used on the construction of these homes that we stripped to the framing, exposing the interior of the walls, showed no wood deterioration.
[ add comment ] ( 207 views ) | [ 0 trackbacks ] | permalink |





We have addressed the accelerated deterioration of New Growth Wood. Old Growth Wood however is many more times durable than New Growth Wood, to the extent it is hard to multiply the difference for explanative purposes. Old Growth Wood is so many times more durable than New Growth Woods, and even new age composites, that we do not advocate its removal or replacement unless it is necessary.
We have remodeled the exteriors of many older homes, the oldest of which dated circa 1703. In the experiences we have had, Old Growth Wood holds up for centuries even in the absence of paint. The density of the wood seems to give it a definite resiliency and resistance to microbial and insect invasion.
Old Growth Wood trim is usually restorable with scraping and sanding and putty application. The siding that has weathered usually will degrade faster than the trim. With settling of the home, newer interior heat installation and the condensation that bombards the siding from the backside, the old weatherboards will go first. They also catch much more of the weather than the trim. The successful adhesion of paint is usually an issue. New age paints are of very high quality and they form a barrier that prevents the natural breathing of the siding. This fact combined with new window installations and heated interiors, the pressure from within a structure pushes the moisture outward to condense on the backside of the paint. This often leads to pockets of moisture and a releasing of large patches of paint.
The wood often comes off in fairly good shape and we have had wood restorers take the product from the work-site. We simply remove the old siding in order to gain access to the walls to insulate them. We install the vapor barrier toward to inside of the home and then install a rigid foam board over the bat insulation. We then install our pre-finished fiber cement siding over the rigid foam. The old trim is left intact and refinished. Sometimes it is cost effective to remove some crown moldings and replace them as they can be very hard to refinish.
[ add comment ] ( 91 views ) | [ 0 trackbacks ] | permalink |





New Growth Wood – Accelerated Deterioration
We have seen accentuated rotting in wood construction materials. These are usually wood framed constructed homes dating back to approximately1988. Cedar Sidings and Roofing are almost always deteriorated beyond viability (with some exception to be discussed further). The quality of lumber has diminished considerably in the latter days of the twentieth century. We are soliciting industry professionals to post here so that we can do more than speculate, as the lumber industry has a tight lid on the causes of what we are seeing in the field.
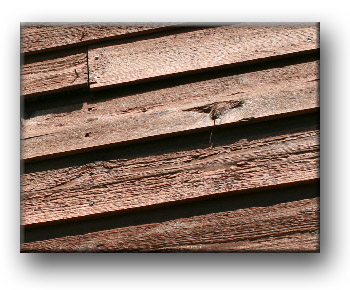
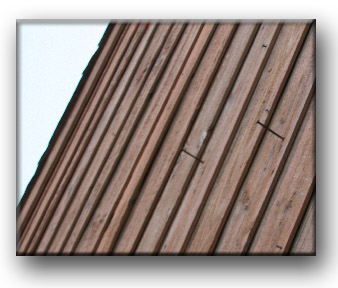
This type of siding used to last for a very long time, even known to be in service after 100 yrs. New growth fails in 15 years.
[ add comment ] ( 156 views ) | [ 0 trackbacks ] | permalink |




