There are even approval processes that a company must endeavor to complete to be approved as a “Green Contractor.” All this just muddies the waters of the true meaning of Green. Similar to the municipal recycling business, where evidence of a truly confused system has been established to validate a government rebate system in these United States of America, where the end result is not 100% recycling. The almighty dollar rules at every turn. In some areas, brown paper, newspapers, cans and bottles are recycled. Some areas, paper is not recycled because a threshold is reached at just the bottles and cans. I have seen it as I have traveled the roads of the northeast.
It is hard not to develop a cynical outlook at what is a lie being perpetrated on the American public. Once, I remember, somewhere in NY State, a massive and rewarding recycling program by school children was tarnished by the lie. An award was being given out complete with luminaries and media present for the filling of dumpsters of cans and associated debris for recycling.
A couple of the enterprising media types followed the dumpsters as they were carted away to the landfill! Yes, the landfill! It was cheaper just to dump the debris than to return it into the manufacturing process. The almighty dollar rules over good judgment. This book will not only endeavor to explain common mistakes made in my industry, but to fight back against the “dollar rules” attitude in home improvements.
A 300 million dollar plus industry, the home improvement money spent is wasted in large part by the consumer. Most of this waste is caused by the “fast food” mentality of the day. We all want it now and we want it right and we want it at an affordable price. All of these elements are subjective, however the metaphor listed above regarding the slap at the children’s efforts at recycling is a slap you should not want for your efforts to improve your home.
[ add comment ] ( 120 views ) | [ 0 trackbacks ] | permalink |





We ask the question because it seems the world wants to capitalize on this new idea of “Green.” An argument seems to be made for every product out there being Green. Green construction is defined by two major characteristics:
1. The amount of strain or stress on the natural environment or resources in the manufacture of the product. The ability to recycle the product upon replacement would conceivably be of concern as it goes to the environmental impact of said product.
2. The sustainability of the product as it relates to life cycle and potential replacement is a major concern. The future burden put upon the environment and resources also falls under this idea of upkeep and sustainability.
Using these two criteria to gauge a building product, some have built upon these ideas with new age thinking. The so-called greenhouse gasses a product’s manufacturer would produce, which if this is important to you, will be commented on for your benefit below.
Slate Roofing
This type of roofing is about as Green as you can get because of the longevity of the material. Slate that is obtained from the Vermont – NY border is still very abundant and very pure. Purity of Slate is a real issue as the Slate from the current veins in PA is not as pure as the northern veins.
Issues with a shorter life cycle of the PA Slate are well known. It is not unreasonable to expect the PA offerings to last from 50 to 100 years. The latter time-frame is rare. The old veins from the Peach Bottom area are now played out. Peach Bottom Slate was regarded as the finest in the world when it was available, lasting 200 years in some cases.
Vermont and NY Slate are from the same area of a swath of real estate of about six miles wide by twenty miles long, with some deviation in the runs of the veins. All kinds of colors are available and some of the offerings last almost as long as the old Peach Bottom Slate.
This would satisfy even the most conservative of conservationists as far as the sustainability of the products. The quarrying of the product may bother some folks as the land is disrupted, but from a practical standpoint Slate is a Green product. The quality of the cut and installation must be ensured as there is no warranty on natural products. Warranties have become for the practical among us, more a list of limitations than actual coverages.
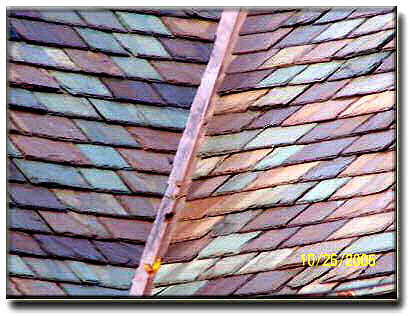
Whether it is Vermont Green, Purple, NY Red or any of the variations, Slate is Green if derived from a northern vein. We prefer Vermont because it is still geographically desirable, readily available and the cost is reasonable.
Imitation Slate
Much is being stated regarding imitation Slate and the warranties of 50 years have the attention of many in the industry. The big push for these products is not for their longevity but for their ease in application. A careful research of the companies that have produced these products and gone out of business would yield an uncertainty regarding the expected life cycle. Remembering that warranties are usually limited, one should look at the company affording coverage before purchasing these products. As quality in workmanship is paramount in the viability of a roofing system, one should ask that if the only reason to install a product is because it speeds installation, where the savings in a job would be realized in the long run. There is a definite savings in using these products, but one should consider the cost vs. life cycle argument. These faux Slate roofs cost more in material expenditures than that of a real slate roof. These savings are real and realized from the labor savings. Installation with the use of nail guns and with new age construction methods allows the virtual novice to install these roofs. Arguments will be made regarding the value of factory training but these claims are made by the purveyors of these products.
Longevity of these products has not been proven. It is only the warranties that provide any perceived safety in the use of these products. The depth of the pockets of the manufacturer must be validated as well as the funds put aside for warranty claims. It was so bad for the consumers that were stuck with roof failures, caught without service that they had to resort to class action suits. Since they were chasing companies going out of business that the federal government did mandate that some of these companies, purchased for peanuts by larger conglomerates, put aside large sums of money to cover future complaints.
The manufacture of these products does require use of natural resources and for the greenhouse gas worriers; these products would not be considered Green. For the pragmatist the higher cost of these materials along with the uncertainty that surrounds them would even supersede any concern for a Green label. For the environmentalist, the life cycle and potential recyclables derived from dismantling a faux Slate roof and the support of the petrochemical "greenhouse gas" producing industry, Green may not be an applicable term, even if limited as used in the context of this article.
Tile Roofing
The wide spread use of tile roofing is indicative of its lasting value. Although new products may not be of the quality of the older imported tiles. Terra-cotta, the most common is expected to last the longest of any sloped roofing system. The older tile can be reclaimed when the nails and flashings give out and reinstalled for another expected lifetime of service. If one figures about a 30% loss on a given job the figure usually rings true and accurate for the amount of replacement tiles needed for a reclaiming effort. Taking an older tile along with a new tile and dropping them onto a hard surface usually ends in the new tile shattering and the old original tile only chipping or even bouncing. This is a true test of Green, but a manufacturer may want to chime in if the new tile is expected to harden further with age. It is preferable for a roofing purest to use a product with true head-lap, such as some slate style tiles. Some tiles compensate for the lack of head-lap with channels in the tiles. No matter the color, tile roofing is Green.
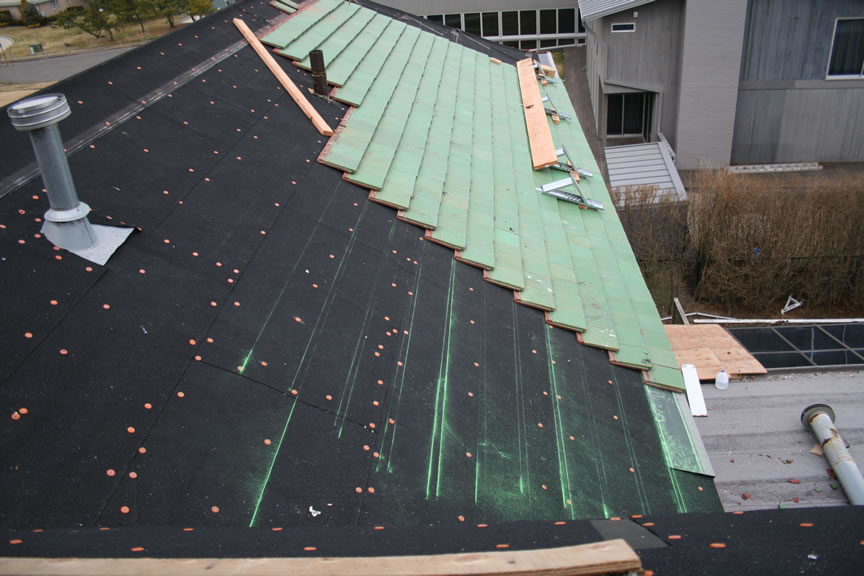
Cedar Roofing
The roofs of old with the old growth cedar shakes and shingles did last a long time. The general life cycle ranged from the low side of 40 yrs. to the high side of 70+ yrs. A fact of lie today is the use of new growth cedar in the industry. A mention of the fact would be hard-pressed to find within the industry. This information is not often revealed to the purchaser of cedar products.
Warranties are offered for treated products and in the range of 50 years. One should read the warranties and also consider the look of the treated products. There is no viable information known to this author as to the increased viability of treated cedar roofing.
It is the experience of the roofers of this company over the past thirty years to expect a cedar roof installed in the past 25 years (circa 1985) to be new growth and have an expected life cycle of 15 – 20 years.
It used to be accepted in the roofing world that a cedar roof should be left alone until dead. The roofs were of such high quality that no maintenance would help and was considered wasted money. This was true regarding old growth cedar. New growth cedar however, can be seen weathering at different rates and one defining factor has been the application of UV and anti-bacterial protective coatings. They do seem to work quite well on new growth cedar. Life expectancy is certainly lengthened with these after market coatings.
The Green aspect of cedar as a roofing material and if of importance should be weighed out as to the projected and expected life expectancy, separate and apart from claims of those that derive income form the product’s use. In the application of Cedar as a roofing material, the desire of the aesthetics usually outweighs any concern for the Green aspect of the product.
Asphalt Roofing
Asphalt roofing has been around for a long time. The cost of the roofing system seems to be the most important factor to a client, bringing in a different context to the word Green. As for the longevity of an asphalt roof, many complaints have arisen from the fiberglass roofing shingle. More can be read regarding the fiberglass generation of these products. It is the multi-layered fiberglass shingles that afford a longer life expectancy. The 30 yr. roofing shingle can be a crap shoot as to the expected life cycle, while the lifetime offerings are more formidable.
The reported asphalt usage, mainly derived form Venezuelan Crude may be of patriotic concern to many folks. The petrochemical industry is a necessary evil to some and to others just a fact of life. It is the wise utilization of natural resources that we will comment as it relates to Green Construction. The lifetime offerings installed by a very critical installer of quality roofing seems to qualify as Green in this context. This may be arguable as with any product in this article.
Metal Roofing
The use of metal in modern roofing has been a mainstay for centuries. The use of aluminum in the modern arena has proven to be problematic in many applications primarily because of the thermal properties of the products. Edgings used in other roofing systems have held up very well because of the relative size of the products combined with the hard fastening of them. Aluminum as a sheet good in large scale and applied as a metal system, or even valleys on sloped systems, tend to move drastically and these materials are hard to seam with any expectation for lasting performance. Material blow-offs are common with commercial aluminum jobs because of the thermal movement properties. Manufacturers will always make the claim that the fault falls on the installer of the products and this may often be true.
Steel and copper are products that have lasting value and are very malleable, according to the particular alloy used. Steel and Copper standing seam roofing in an authentic, double hemmed seam with blind fasteners installed onto viable slip sheet (for thermal movement allowance) are very long lasting roofs. One can expect these roofs to last for well over a hundred years. This is referring to an “authentic” standing seam application and not the “snap-lock” and faux applications of today. The former types of installations often fail either from installer error (as the push for these products is for the ease of application) of because of wind uplift. New commercial seaming machines have made the job easier but the panels should be carefully specified if over 10 ft. Some lower sloped roofs have worked quite well in the steel versions with long runs and extreme allowances for thermal movement. Tern coated steel is one of the finest roofs that can be installed and the use of stainless has also proven to be a very long lasting roofing system.
So as for Green application, the subjective person may fall on either side of the argument, but for longevity, properly fastened copper and steel are winners in the metal markets. We say “properly fastened” as direct mechanical fastening of these materials may yield unsatisfactory results.
Note: Check our website for the current thinking of use of copper under and cedar runoff and mixing if with any material which will provide a potential chemical reaction with the metal.
Low Sloped Applications
The use of steel panels is listed above under metal roofing. The Green-ness of a given roof application on a low sloped roof may just boil down to cost vs. value. A good contractor is of major consequence on these applications. The best low sloped applications may not be practical. A stainless steel, seamed and soldered over a good substrate with a slip sheet will last lifetimes but the sq. footage will dictate the practicality of the use of this metal. Copper will also last a long time along with tern coated steel. The new tern, a zinc/tin will develop a patina that is an appealing gray.
Asphalt and rubber offerings do the job and the longevity of the given products vs. the predominance of acid rain and irritating pollutants have to be weighed against a proven system. Again the depths of the pockets of the manufacturer and the quality of the installer have to be considered above all issues. The Green aspect of a low sloped roof would remain attributable mainly to the length of time a roof will last given all variables of concern.
Gutters
Although aluminum has maintained a major market share in the industry, copper remains the Greenest of all. Not only for its anticipated 10 yr. patina cycle, but for its ability to gracefully move through its thermal changes (provided rigid alloys are not used with direct fastening), its workability and ability to be seamed with a lasting solder seam and its perceived value it lends to a property does copper win in the gutter arena.
Copper gutters last and even though they are not as rigid and formidable as galvanized gutters, the combination of the permanent seam along with the look of the metal makes copper is a clear winner. Copper is expensive, so the Green consideration may fall secondary to cost effectiveness. One should consider however that copper will last twice that of aluminum without the growth of organic algae material that clogs all gutters eventually (even if you install a screen or covering). Copper’s natural anti-microbial properties have been well known for many centuries. Green it is as it becomes with age!
Vinyl Siding
We have to be careful here because we have been threatened by the Vinyl Siding companies in exposing any true and honest deficiencies in their products. We have published our thoughts on the use of ‘J’ channels and how they make for leaks behind siding. Also the industry’s own public statements for mandatory underlayments in the “flashing” details seem to speak for themselves. A Green approach would be to secure a sound cladding that provides a true watershed and would last a lifetime. We encourage consumers to look beyond the immediate cost and to the real and anticipated life cycle of the product to be installed. The ability of the product to be recycled is important. To this latter attribute for which vinyl has strong potential, we can attest as have recycled a lot of it. We will let the reader make the judgment as to the Green aspect of this petrochemically produced modern day cladding material.
Wood Siding
The idea of using new growth wood siding would parallel that of wood roofing. Wood siding will last about the same time as the roofing but without as much of the microbial activity as the roofing. This would suggest that wood is harmed at least as mush by UV rays as it is moisture, bugs and microbes. You can paint it Green if you want.
Fiber Cement Siding
Some manufacturers of these products have a proven track record and industry experts anticipate the sidings should last 100 years. This is not true for all of the manufacturers as the methods to produce the materials, the coatings used and the actual physical properties differ dramatically. These products are in flux and only an astute and careful installer with a lot of experience can deliver a truly Green siding job with fiber cement siding. The industry has grown so rapidly that consumers should beware of the products’ deficiencies and seek guidance from a company that puts quality before any allegiances to particular manufacturer. Green, most certainly if the right product and the right installer are used in the production of a sound wall system.
Composite Trim
Composites for sidewall application are nothing new. Trim application is where the current money is to be made. There is a section on PVC trim in this forum. We have used every conceivable type of composite trim on the market today. The fiber cement trim is most desirable, but for its short 10 ft. sections, difficulty in obtaining delivery without loss because of broken pieces and the weight of the product. Once in place fiber cement trim along with a number of non-PVC composites are very stable and will last for a long time if properly coated and pre-treated in the field. Many of these are made from recycled or even post-recycled materials which should be of great interest to the super Green consumer.
Aluminum Wrapped Trim
The use of aluminum fabricated capping has just about run its course in the USA. The combination of new growth wood along with a capping that traps moisture makes for replacement in short order. The cost of aluminum alone along with labor makes for an attractiveness of the solid cornice replacement of new growth wood. Old growth wood should never be capped and after the aluminum begins to fall off, the consumer can consider the folly of ever capping it in the first place. Is aluminum capping Green? Only if it is green is it green at all, but for the wise it is a waste of time and money and resources.
Polyurethane Trim
The greenhouse gas folks will have to chime in on this one. The “PUF” trim as we know it, is expected to last about 20 years. It usually has a thin coating and it is soft and the older versions of the products have yellowed in the field. Is it Green? You be the judge.
Stone & Faux Stone
The jury is still out on this but on partial walls, both stone and faux stone applied in mechanically fastened, fully adhered sections seem to last the test of time. Entire walls on non-screen wall applications should be reconsidered as it is possible that moisture may not be able to escape entire wall sections. A carefully applied wall of veneer should not fall victim to external moisture but internal moisture in the winter months. The lower moisture absorption rate of the new materials (barring some of the natural stones in the industry used primarily on full brick ledges, etc.) for application as veneer walls combined with proper underlayments (not house-wraps) will yield lasting results. We must stress a conscientious interior vapor barrier be installed in dry conditions for the proper protection of the wall system during winter months. Partial walls are preferable as they afford the better release of any resident moisture. Are stone veneers Green? Yes they are if properly installed with interior concerns taken seriously.
Brick and Stone
Real brick and stone placed on a brick ledge (part of the foundation provided for the weight of the masonry wall) usually have a 1” space between the wood framed wall and the veneer wall. Unless a true brick or stone house is in question this is the norm. A true stone or brick house usually has an interior wall. In the case of a real brick house, a “row lock” (bricks running perpendicular to the wall to connect both interior and exterior walls – sometimes faux row-locks are placed in the courses circa turn of the 20th century) is run every ten courses or so. This course can also be applied as a “dummy” on screen walls to mimic real brick homes.
It is the underlayment and the flashings on these installations that are crucial. First is the underlayment. Underlayment is not flashing! Underlayment is never to be considered flashing! Contrary to the beliefs of many in the trades and even those in the architecture fields and specifiers and manufacturers alike, underlayment is underlayment only. A temporary protection in times of inclement weather and a protective measure in times of extreme weather or if a leak in the primary protective layer should fail are the reasons for underlayment. Second is flashing and flashing is metal! Metal, preferably copper but in some areas aluminum is used (but not recommended) in an inter-course weave that directs 100% of the water out provided weep holes. So often the importance of both underlayment and flashing are overlooked. Often the mason will dump his mortar into the 1” space provision, thereby eliminating the gap, creating a bridge and inviting water intrusion into the wood framed wall.
Getting back to Green, the topic of this posting, Brick and stone are certainly Green if done properly. Lentils do rust and expand after many years and the damage can cause major cracks. With proper upkeep, this can be averted and brick and similar stone veneers can last a very long time.
Plywood vs. Solid Planking
Several implications have been made by the old-timers regarding the quality of plywoods. Comparisons have been made to solid planking. The problems with the analogies and comparisons made are that they are behind in the times. Never have exterior grade plywoods been better than they are today. Never has the quality of solid planking been as poor as it is today. New growth wood and better quality plywood are the reasons for this change in the marketplace. Plywood does last if moisture is controlled. Moisture from, say a slate roof should shed off the roof with the possibility of dew at times of temperature change rising up and under the slates. The underlayment will pick this moisture up and take it away mainly by dripping it back out and onto the roof. The underlayment will last for as long as the roof as it receives virtually no UV radiation. The moisture from the attic should be nil, but if present it should not be significant enough that simple ventilation would not enable dissipation. If moisture is not a problem from above (good roof) or below (good ventilation, attic insulation, tight living area and vapor barrier, the plywood will last as long as the slate. New growth solid planking has a very low resistance to even minimal moisture. Unlike old growth wood that can take an enormous amount of moisture before deteriorating, new growth begins to deteriorate very quickly.
So is new growth solid planking Green? How about plywood and its resiliency that far exceeds new growth wood? We would say “No” and “Yes.”
Underlayments
It is impossible to tell as to the Green-ness of underlayments with the exception of real Asphalt Saturated Felt (tarpaper). There has not been enough time to tell the significance of many of these new age underlayments. Claims of permeable abilities are not clear as in the removal of many claddings, these newer underlays have not been as formidable, or as permeable as tarpaper. How could this be? There is something about the layers of tarpaper that tends to carry moisture and not trap it. The tighter methodologies of modern exterior cladding, especially in retrofitting applications, leaves much room for trouble later on down the road. The interior is the place for a tight vapor barrier. Even though an exterior underlayment is claimed not to be a vapor barrier, complete with a good perm rating, it becomes just that in the presence of moisture and a colder exterior temperature, actually creating a dew point and becoming a vapor barrier. We have found it in perfect condition well over a hundred years after installation. This is more than we can say for many other types we have found failing after twenty years. This is not to say that new underlayments can be superior to tarpaper, but we advocate what we know to work.
Tar Paper is Green even if it is black.
[ add comment ] ( 237 views ) | [ 0 trackbacks ] | permalink |




